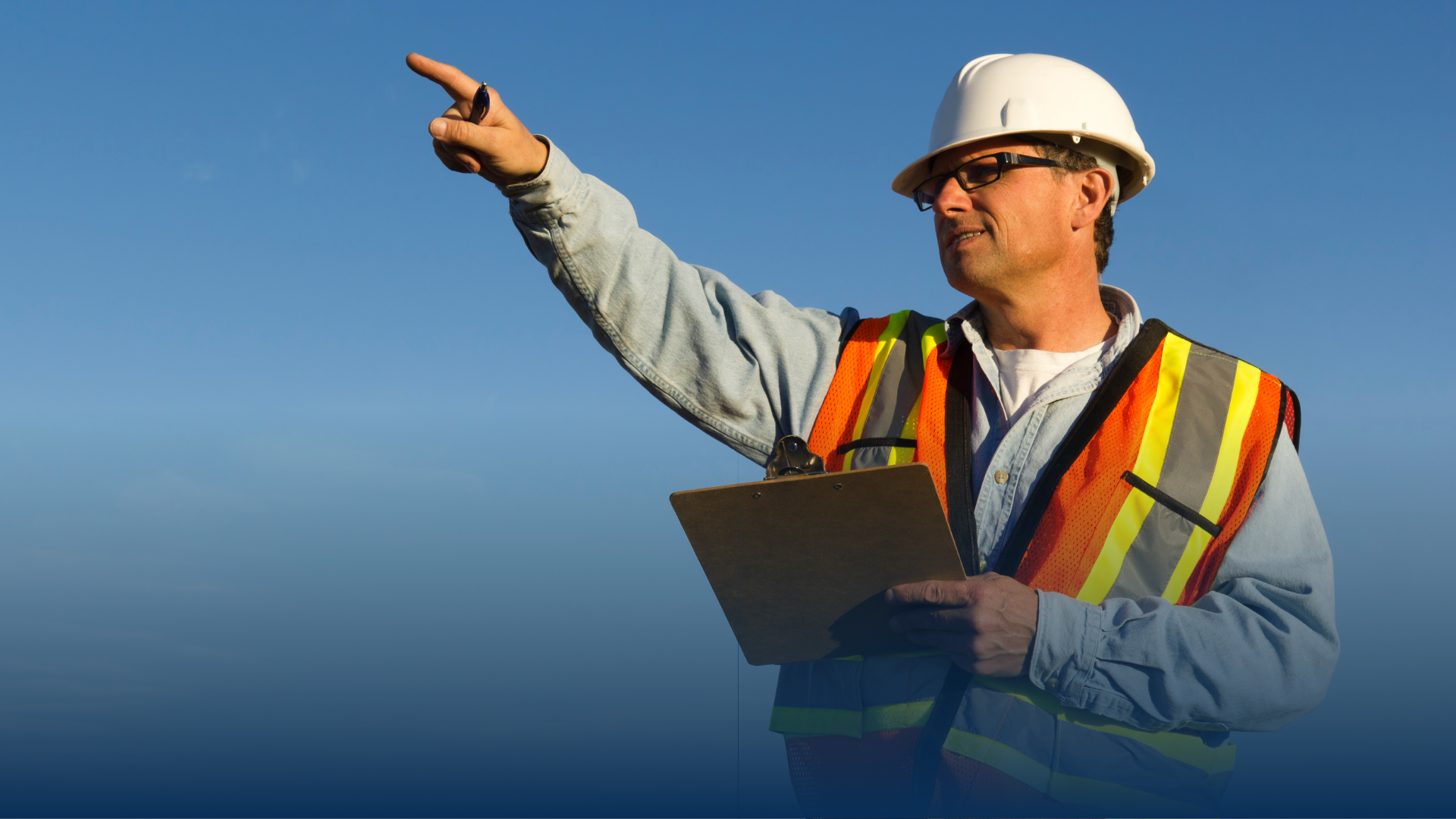
Workplace safety is a fundamental priority for every organization, ensuring that employees work in an environment free from harm or injury. One of the most effective frameworks for achieving this goal is the Hierarchy of Controls. This concept organizes safety interventions in a prioritized manner, focusing on eliminating hazards at their source before relying on less effective measures.
What is the Hierarchy of Controls?
The Hierarchy of Controls is a system used to minimize or eliminate exposure to hazards. It is structured in a pyramid-like format, where the most effective solutions are placed at the top, and the less effective ones are at the bottom. The primary goal is to address the hazard in the most comprehensive way possible, focusing on eliminating the risk entirely before considering other options. The hierarchy is divided into five levels, each representing a different method of control, which are listed from most to least effective:
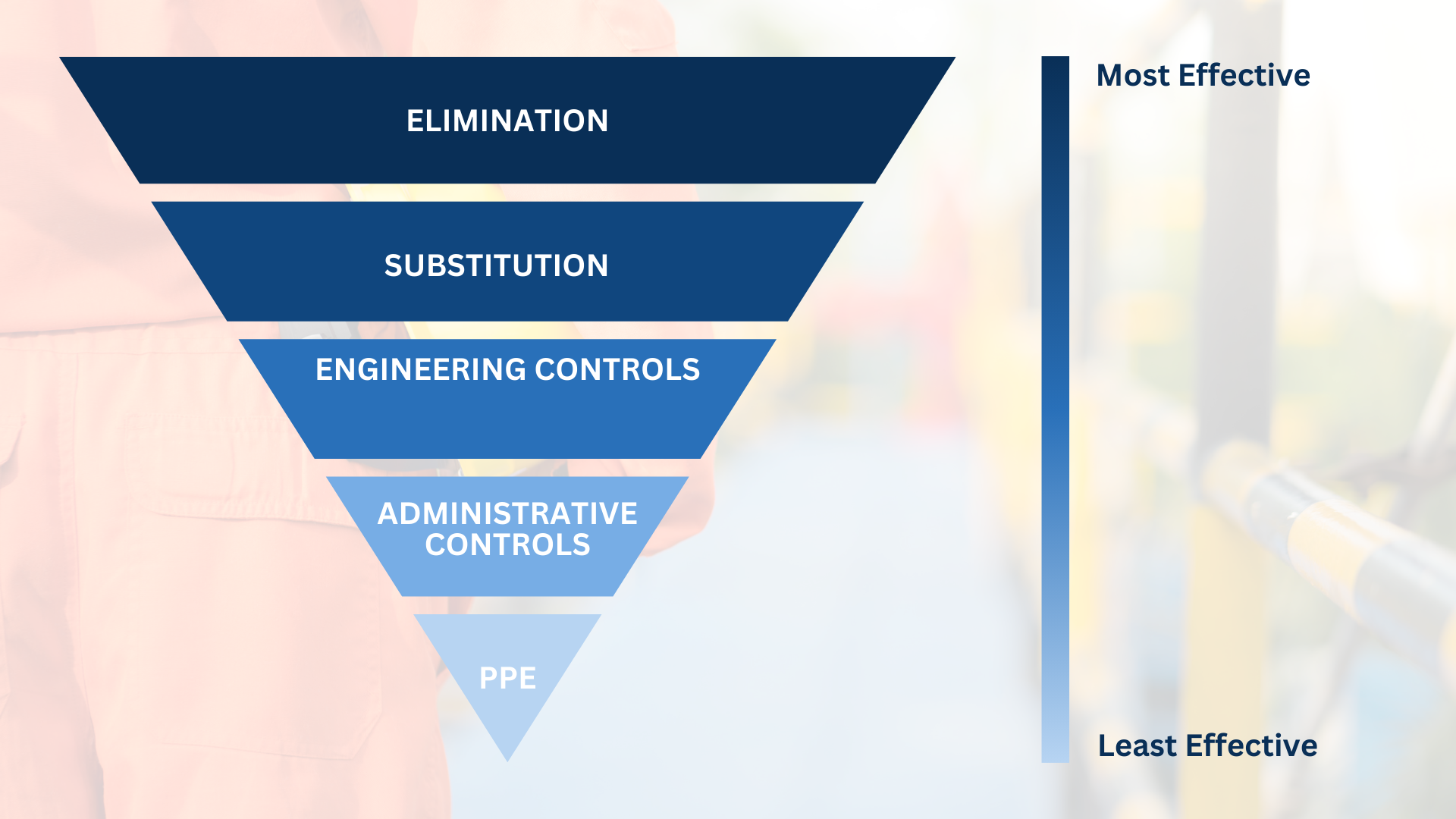
- Elimination
- Substitution
- Engineering Controls
- Administrative Controls
- Personal Protective Equipment (PPE)
Each level of the hierarchy builds upon the previous one, aiming to mitigate the hazard as effectively as possible.
1. Elimination: The Most Effective Control
At the top of the hierarchy is elimination, which involves completely removing the hazard from the workplace. This is the most effective approach, as it entirely negates the potential for harm.
Example: If a factory uses hazardous chemicals in its processes, the best solution would be to eliminate the use of these chemicals altogether. By finding an alternative production method that does not involve dangerous substances, the risk of exposure is eradicated, ensuring a safer environment for all employees.
While elimination may not always be feasible in every situation, it should always be the first consideration when addressing workplace hazards.
2. Substitution: Replacing the Hazard
If elimination is not possible, the next best option is substitution, where the hazardous material or process is replaced with something less dangerous.
Example: In an environment where workers are exposed to toxic fumes from a certain solvent, substituting the solvent with a non-toxic alternative can significantly reduce the risk to health.
Substitution is an effective control measure but still leaves some level of risk, depending on the substitute used. Thus, it is considered a step below elimination in terms of effectiveness.
3. Engineering Controls: Reducing Exposure
When elimination or substitution is not possible, engineering controls become the next step. These controls focus on isolating workers from hazards by designing safer systems and equipment to minimize exposure.
Example: In a manufacturing plant, installing ventilation systems or using enclosed machinery to contain hazardous processes can help prevent workers from inhaling harmful substances. Similarly, using soundproof enclosures around noisy equipment can prevent hearing damage.
Engineering controls physically alter the workplace, providing an effective method to control hazards without relying on human behavior. However, they are generally more expensive to implement than other controls and may require ongoing maintenance.
4. Administrative Controls: Managing the Hazard
If engineering controls cannot completely eliminate the risk, administrative controls focus on changing work practices and procedures to minimize exposure to hazards. These controls rely on the implementation of policies, training, and scheduling to reduce the risk of harm.
Example: Administrative controls might involve limiting the amount of time a worker is exposed to high levels of noise, rotating employees in and out of noisy environments to prevent hearing damage. Other examples include establishing strict safety protocols, providing regular safety training, and using signage to warn employees of potential hazards.
While administrative controls can reduce risk, they are dependent on human behavior, making them less reliable than engineering controls. They are also more prone to being overlooked or improperly followed.
5. Personal Protective Equipment (PPE): Last Line of Defense
The final level of the hierarchy is Personal Protective Equipment (PPE), which is used to protect workers when other controls are not sufficient to eliminate or reduce the hazard. PPE serves as the last line of defense, providing physical barriers between the worker and the hazard.
Example: In construction, workers may be required to wear helmets, gloves, safety goggles, and high-visibility vests to protect against various hazards, such as falling objects, sharp tools, or machinery. Similarly, in chemical plants, workers might wear protective clothing and respiratory masks to prevent exposure to hazardous substances.
While PPE is essential for protecting workers, it is considered the least effective form of control because it does not address the hazard itself, only its consequences. PPE relies on correct usage and maintenance, and even the best gear can fail in extreme conditions.
Why the Hierarchy of Controls is Critical for Workplace Safety
The Hierarchy of Controls is a vital tool in workplace safety because it emphasizes the importance of addressing hazards at their source. By starting with elimination and working down the pyramid, organizations can reduce the overall risk of harm to workers. Here’s why it matters:
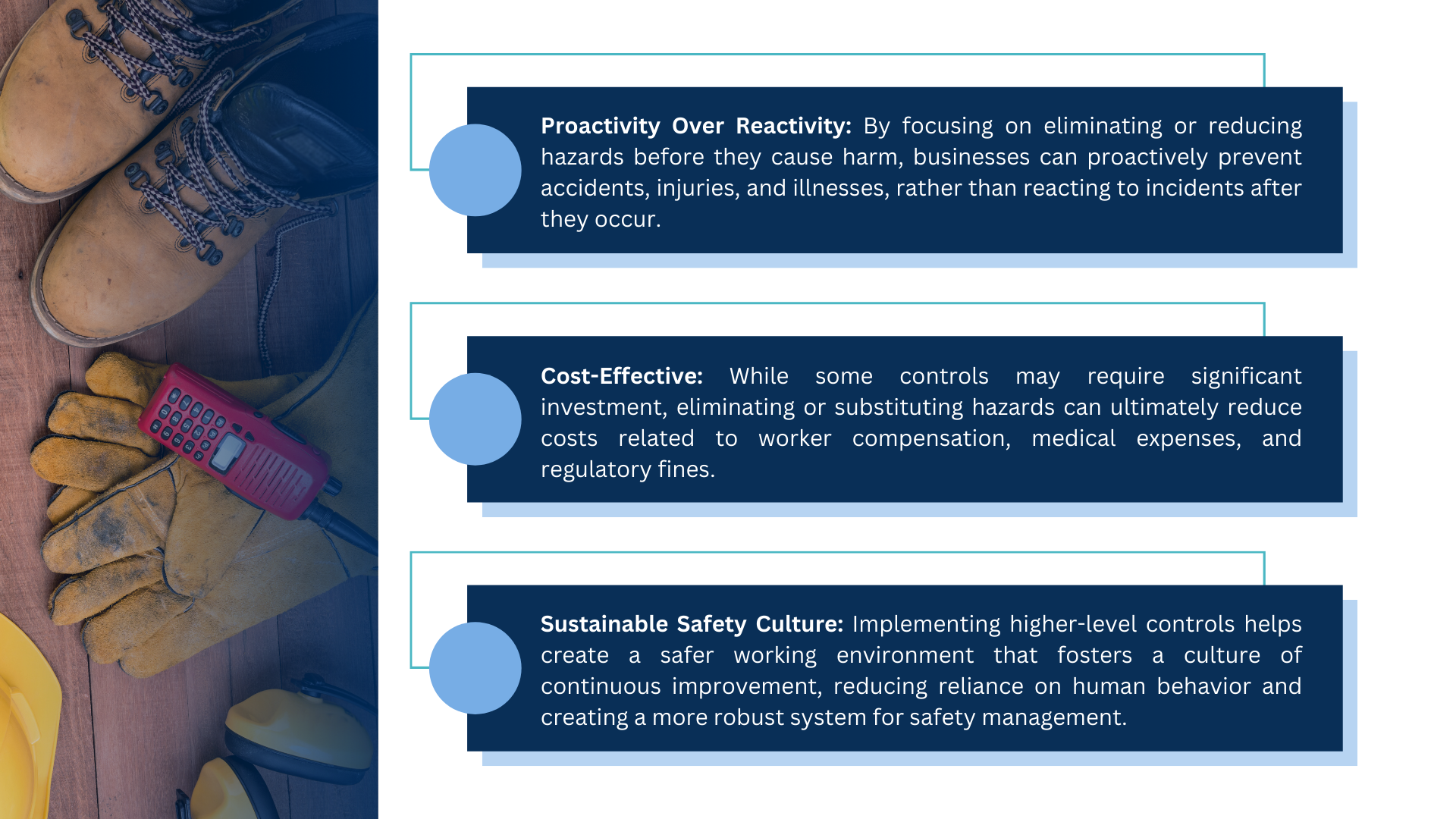
Applying the Hierarchy of Controls in the Workplace
To effectively apply the Hierarchy of Controls, organizations should assess risks regularly and prioritize actions based on the severity of the hazard. A mix of controls from different levels will often be required to ensure comprehensive protection for workers. For example, eliminating a toxic chemical might be possible, but engineering controls such as ventilation systems may still be necessary for other hazards. Workers should be involved in safety discussions, and training should be provided to ensure they understand the purpose and importance of each control measure.
Conclusion
The Hierarchy of Controls offers a structured and systematic approach to mitigating hazards in the workplace. By prioritizing elimination, substitution, and engineering controls over administrative controls and PPE, companies can ensure the highest level of protection for their workforce. It is a proven strategy that reduces the risk of injuries and creates a safer and more productive work environment, ultimately benefiting both employees and employers.