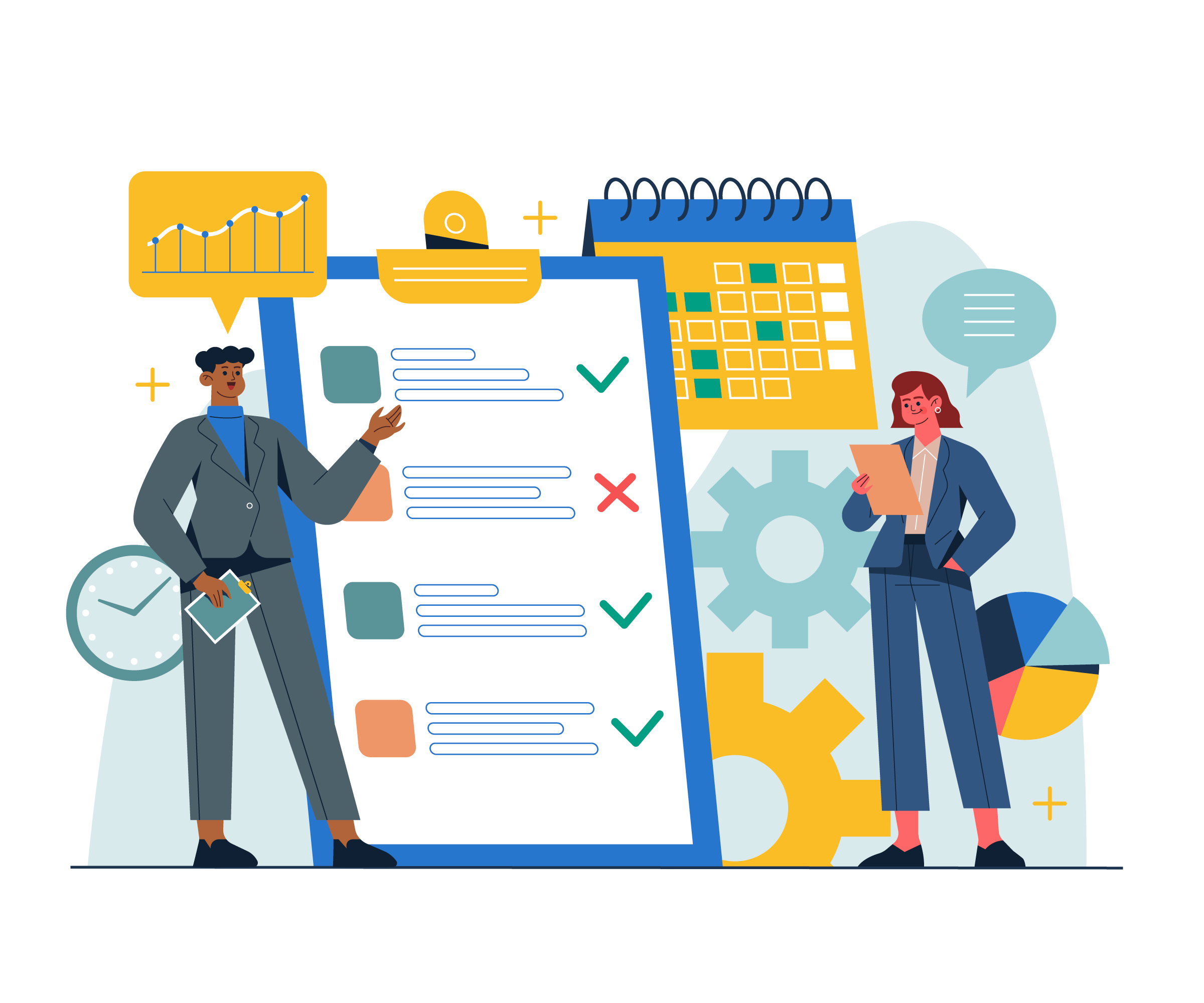
When an accident occurs in a workplace or a product faces failure or machine malfunctions, the first instinct is to initiate a rigorous process of investigation to understand why such unfortunate incidents occurred. Corrective and Preventive Actions, commonly known as CAPA, is that particular process or strategy that methodologically strives to mitigate risks, identify the source of the problem (whether actual or potential), understand the root cause, introduce necessary measures, and document the current happenings to avoid encountering similar features in the near future.
The CAPA approach is essentially comprised of two basic elements
- Corrective Action - Aimed to eliminate the major cause of a ‘detected’ problem
- Preventive Action - Seeks to put an end to the causes of ‘potential’ problems.
CAPA in Pharmaceuticals
Now you might be wondering what is the relationship between the CAPA system and pharmaceuticals. The bond that connects these two is the desire for safety. Pharmaceuticals by their very nature are laden with dangers. The CAPA system plays an integral role in quality management, identifying dangerous situations related to products or processes and preventing their recurrence. For example - defects in the sealing process led to the destruction of the medications. CAPA would analyze the situation and propose corrective actions to solve the sealing problems and take steps to avoid reputation in the future.
When is CAPA triggered?
- Non - Conformity
Non- conformance or deviance refers to the failure to fulfill mandated requirements. This can occur at both the product level and the process level. Such events may be the result of negligence on the employee’s end or due to defective equipment.
- Customer Complaints
Instead of identifying the problem during the manufacturing process, customer complaints reveal deficiencies after the products have been introduced in the market. The defect may pertain to the packaging, the inability of the product to produce desired results, or severe undocumented side effects.
- Audit Findings
Audits, both external and internal are conducted to verify whether existing procedures and systems are aligned with the established parameters. Irrespective of the type of audit, any discrepancy found furnishes enough evidence for initiating CAPA.
Any of the above events may trigger the need to initiate Corrective and Preventive Actions. The purpose of CAPA here is to eliminate the problem and take desirable and appropriate steps to prevent re-occurrence.
Importance of CAPA in the Pharmaceutical Industry
Many pharmaceutical companies would agree that CAPA is a fundamental management tool. With the development of technology, they use CAPA trackers to carry out the required functions.
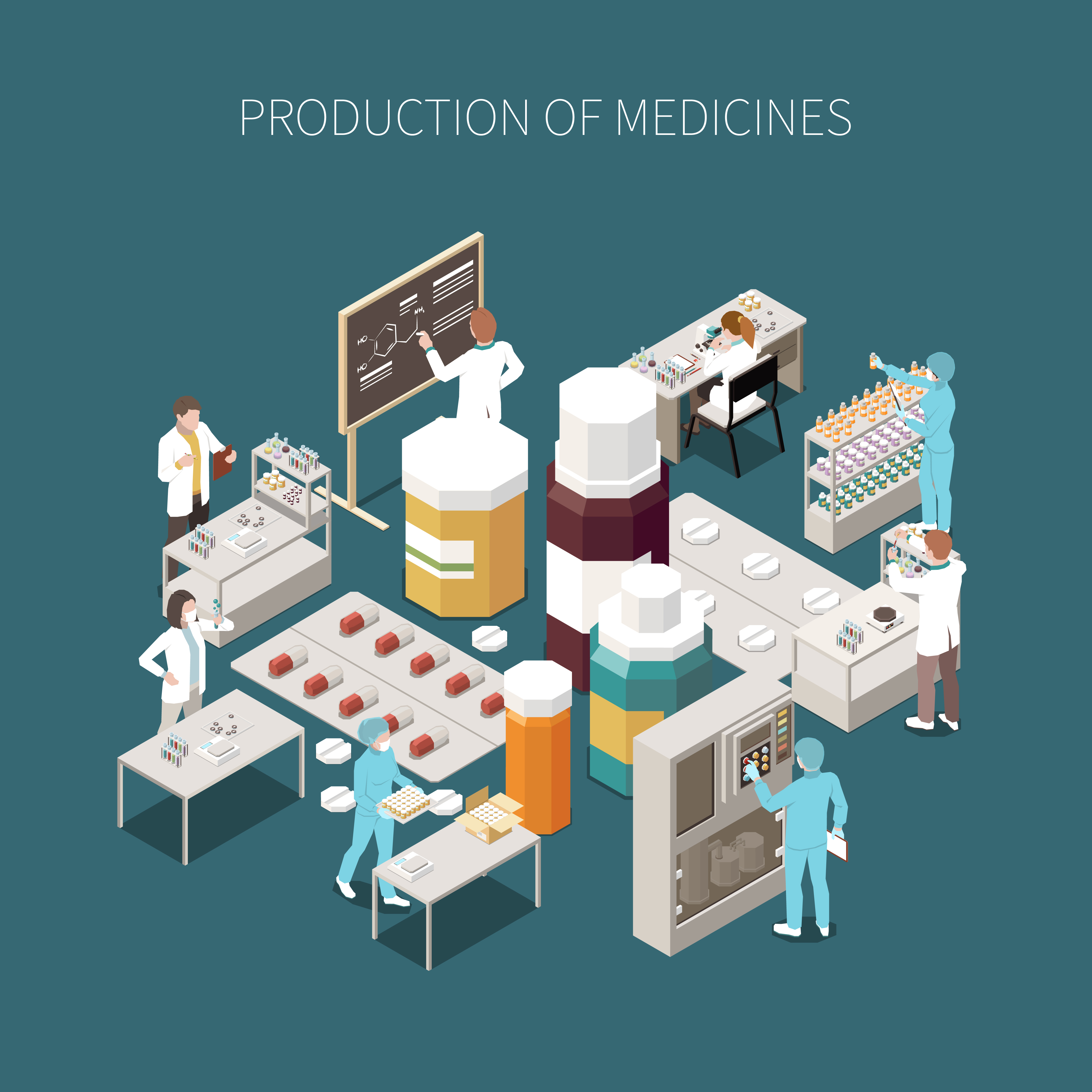
Let us now understand why it is necessary for pharmaceutical companies to undergo the CAPA procedure and how it propels the business forward.
- Product Quality Management
The end goal of any company is to successfully offer impeccable products and services to consumers. Similarly, in the pharmaceutical industry, the production of drugs and medicines holds the utmost priority. Implementing CAPA guarantees that the products are top-notch. It enhances product quality and decreases the chances of failure or defect by identifying and investigating anomalies in the production process at the right time. If CAPA is carried out at regular intervals, with each inspection the quality of the product would continue on an upward trajectory.
- Compliance
Rules and regulations, be it pertaining to safety or manufacturing are put in place to avoid unfortunate incidents and attain the highest level of quality. Compliance with such standards is a necessity for all pharmaceuticals. CAPA is also a requirement for many regulatory bodies, non-compliance with which may lead to penalties. Whether this procedure is carried out without the aid of technology or with CAPA trackers, it makes sure that everything starting from manufacturing to documentation is done in line with the protocols established by the standardized bodies.
- Successful Completion of Audits
Audits are conducted in pharmaceuticals to ascertain the quality, validity, and reliability of the products and processes. It also furnishes reports on the efficiency of the company and reassures the public of the efficacy of the product. As such, it is imperative that the company successfully completes these audits. Timely CAPA means that violations, negligence, non-conformity, etc. would be detected earlier highlighting the company’s commitment to mitigating risks and improving the quality of its products. This means the pharmaceutical company is always prepared to excel at the audits and provide the required documents/reports.
- Holistic Benefits
Along with the above-mentioned reasons, CAPA is necessary for a pharmaceutical because it bears indirect advantages as well. Repeated assessment and inspection assures the optimum quality of the product which fosters and reinstates a positive public image. This environment of reliability and high-quality products also invites an increase in revenue. CAPA can also be credited with promoting overall efficiency within the company as it eradicates problems, reduces failures, and prevents recurrence which ultimately leads to better performance and higher productivity.
Together with Technology
Although littered with multiple benefits, CAPA is a very complex procedure encompassing different actions at different steps. Technology has made this task somewhat easier. With digital CAPA trackers and CAPA management solutions, the process becomes more focused as well as cost and time efficient.
SafetyConnect’s Action Tracking System is one such solution that helps pharmaceutical companies ease the burden of CAPA. With this Action Tracking System, you have access to effective management of corrective and preventive actions at the right time and ensure fulfillment of all audit requirements.
You can book a demo here and unlock the secret to a more efficient and faster CAPA.