
Workplace safety hazards are a critical concern across industries, impacting both individuals and the broader economy. Despite advancements in safety technology and improved awareness, certain risks remain prominent, particularly in high-risk environments like construction, manufacturing, and logistics. Among the most common and dangerous workplace hazards are working at height, man-machine interfaces, and confined spaces. Addressing these hazards requires a strategic approach, emphasizing not only compliance with safety standards but also fostering a culture of proactive risk management.
Safe & Sound - Insights into 3 Common Workplace Safety Hazards
In this podcast episode, Mr. Thanmai Deekshith and Mr. Partha Bhattacharya discussed critical workplace safety concerns. They emphasized the risks associated with working at height, man-machine interfaces, and confined spaces, highlighting the pressing need for enhanced safety standards.
1. Working at Height
Working at height is one of the leading causes of fatalities and injuries across various industries, especially in construction, maintenance, and industrial operations. This hazard arises when employees perform tasks above ground level, such as on scaffolding, roofs, ladders, or elevated platforms. The risks associated with working at height are multifaceted, ranging from falls due to lack of proper fall protection to accidents caused by unstable work surfaces or improperly secured equipment.
Challenges and Control Measures
The meeting discussion highlighted the gravity of fall-related incidents and the ongoing struggle to convince management in smaller construction industries to prioritize safety. Often, cost considerations or time pressures lead to shortcuts, putting workers at significant risk. However, effective risk management can be achieved by implementing a clear hierarchy of control. The priority is to eliminate the need for working at height when possible, such as through the use of ground-level equipment or tools that eliminate the need for ladders. Substitution with safer alternatives, such as scaffolding or aerial lifts, can further reduce risks.
When these measures are not feasible, engineering controls like guardrails, safety nets, and secure scaffolding must be in place. Proper administrative controls—including clear safety protocols, training programs, and regular safety inspections—also play a vital role. Finally, personal protective equipment (PPE) such as harnesses, helmets, and lanyards should always be used to provide an additional layer of safety.
The technological future holds promise for reducing fall risks. Innovative solutions such as wearable safety devices that monitor worker position and alert them to unsafe conditions are emerging. Additionally, virtual reality (VR) and augmented reality (AR) are being explored for safety training, allowing workers to experience realistic height-related scenarios without actual risk.
2. Man-Machine Interfaces
The integration of man and machine is a cornerstone of modern workplaces, especially in manufacturing, construction, and logistics. However, this interface can be fraught with risks if not properly designed or maintained. Inadequate machine guarding, poorly designed control panels, and flawed feedback mechanisms can lead to accidents, ranging from cuts and amputations to crushing injuries.
Challenges and Control Measures
One of the major issues discussed during the meeting was the importance of inspecting safety devices in machines, such as Automatic Safe Float Indicators and limit switches on cranes and conveyors. These devices are critical in preventing accidents, but their effectiveness is diminished when they malfunction or are not inspected regularly. A key point raised was the potential danger of complacency, with some workers or managers overlooking routine checks or assuming that machines are functioning correctly without verifying their safety features.
To mitigate these risks, it is essential to implement rigorous maintenance protocols and routine inspections. Automation and technology can also play a significant role in improving man-machine interfaces. For instance, incorporating safety sensors that automatically shut down machinery when an employee is too close to moving parts can prevent serious injuries.
Moreover, ensuring that workers are well-trained on both the machine's capabilities and its safety functions is critical. The conversation also touched on the importance of using ergonomically designed controls that reduce the likelihood of operator error and make it easier for workers to interact safely with machines. This requires an ongoing focus on both training and design innovation, ensuring that machines and workstations are intuitively designed for maximum safety and efficiency.
3. Confined Spaces
Confined spaces—areas that are not designed for continuous occupancy but where workers may need to enter for tasks such as maintenance, cleaning, or repairs—pose one of the highest risks for injury or death. These spaces include tanks, tunnels, vats, silos, and ducts. The main hazards within confined spaces include the potential for toxic gas exposure, limited airflow, fire hazards, and the risk of entrapment.
Challenges and Control Measures
The discussion emphasized the complexity of working in confined spaces and the need for thorough planning before entry. A key strategy to mitigate risks in these environments is to ensure proper ventilation to prevent the buildup of toxic gases or lack of oxygen. Additionally, strict lockout/tagout procedures are essential to prevent machines or systems from being accidentally activated while workers are inside.
The role of training cannot be overstated. Workers must be well-versed in confined space entry procedures, including proper use of PPE such as respirators, gloves, and fire-resistant clothing. Having a rescue plan in place before entering confined spaces is also crucial, ensuring that emergency services or designated rescue teams can respond swiftly if needed.
The discussion also addressed the increasing role of monitoring technology. Devices that continuously measure air quality and gas levels inside confined spaces are now commonplace in high-risk industries. These tools can alert workers to dangerous conditions in real-time, providing an additional layer of protection. Furthermore, advancements in remote monitoring and drones are helping to assess confined spaces before human entry, identifying potential hazards from a safe distance.
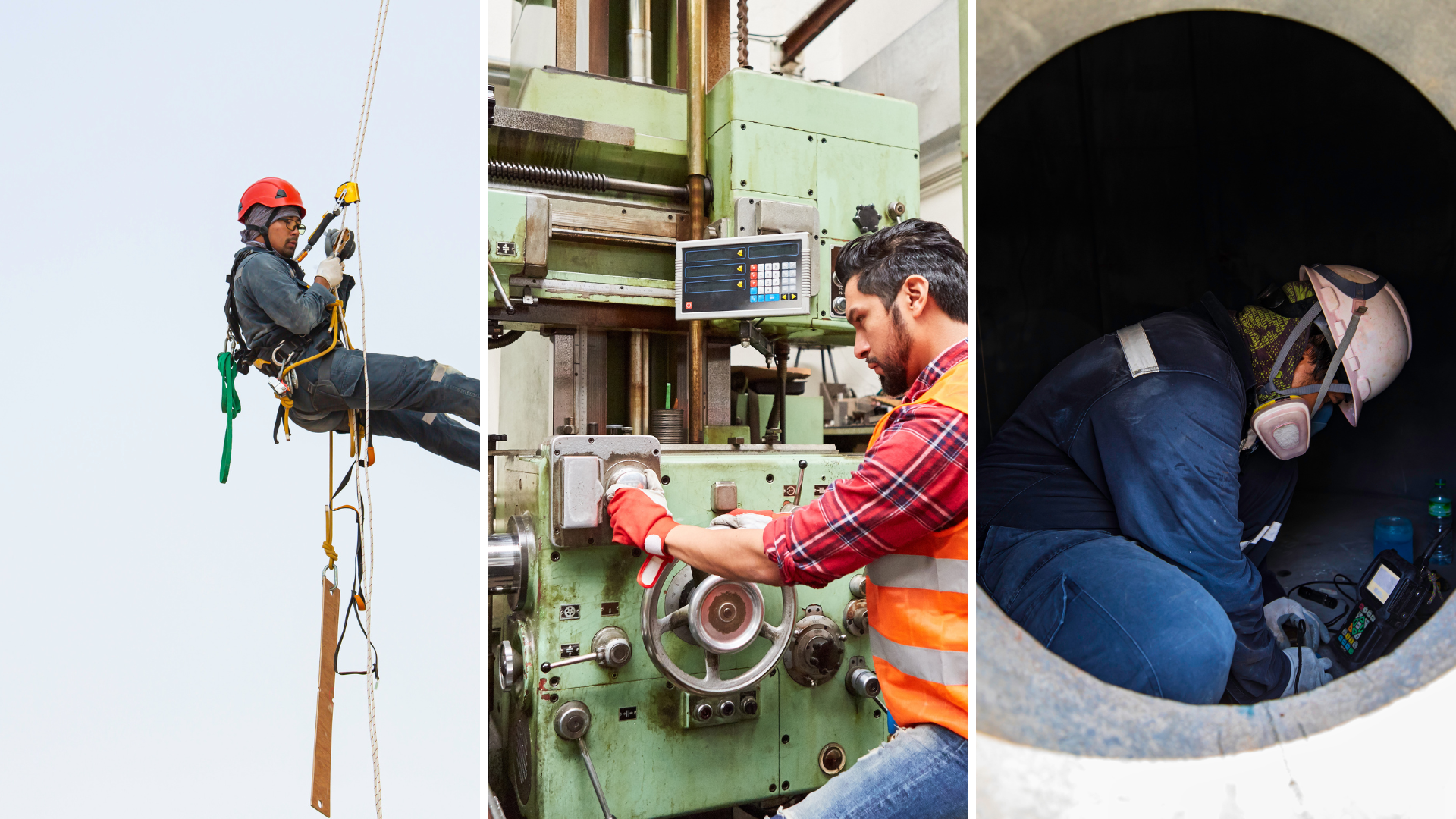
Conclusion
Addressing workplace safety hazards such as working at height, man-machine interfaces, and confined spaces requires a holistic approach that combines effective safety protocols, technology, and training. The insights shared in the meeting highlighted the need for a strong commitment from management, clear safety systems, and continuous innovation in safety technologies. By focusing on these common hazards and implementing practical, well-considered safety measures, organizations can significantly reduce the risks to their workers, creating a safer and more productive work environment for all.