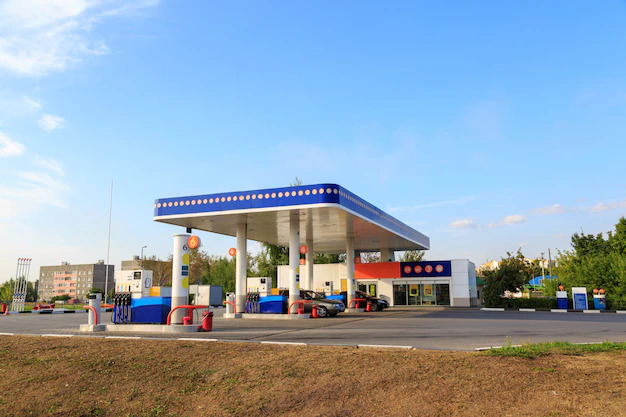
Client’s Overview:
This case study is for our Customer who is a leading Fuel Dispenser Manufacturer. Since the 19th century, the company has manufactured the world’s leading fueling and convenience store equipment and technology. The customer has a big team of field engineers who travel daily to complete the installations and provide support to their respective clients. They have a constant concern for the safety of these employees as there were frequent accidents which resulted in Declining employee morale, cost of replacement, lost man-hours.
Challenges:
- In 2019, 20 major accidents were recorded. Further to reduce this they have introduced Defensive driving training which helped to reduce the incidents by 25%.
- In 2020 they observed again 15 major accidents that triggered a red flag and started looking for a comprehensive solution which not only trained employees on how to drive theoretically but gave visibility on the driver behaviour to analyze the root cause of these accidents.
- Decrease the Man hours lost.
- Employee real-time travel monitoring to have quick response during SOS.
- Lack of operational visibility : Employee productivity, TAT, Driver behaviour during Late home arrivals. Lack of reporting mechanism, visibility and motivation for safe driving.
Solution:
SafetyConnect’s Field Force Driving Safety Solution was a smart fit to address the pain points posted by the HSE team. During the one-month pilot we have provided
- Employee tracking to provide the live location of their vehicles.
- Traveled path monitoring of the employees.
- From no visibility to vivid clarity on driving behaviour.
- Safety Score and unsafe event's visibility in real-time
Metric 1- Driver Behaviour monitoring and Safety Score :
Solution provided the control over the driver behaviour along with the visibility. Daily reports and trends aided to identify the At-risk driver on a monthly basis.
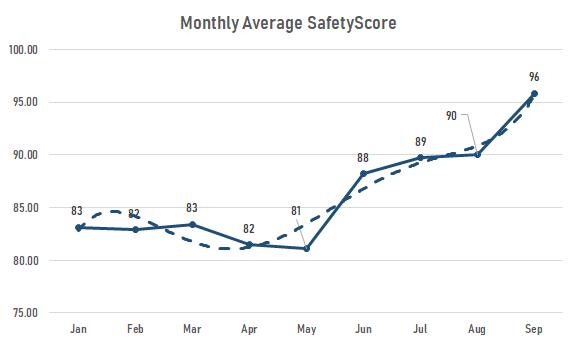
Metric 2- Decrease in man-hours lost:
An organization looks for maximum employee utilization, thus reduction in major accidents has a positive effect in decreasing the man-hours lost.
Reinforcing ~70% decrease in the man-hours lost
Metric 3- Employee Counselling:
Frequent scheduled counselling calls showcased noticeable differences where once counselled employees weren't re-counselled. Also, there has been a significant decrease in the daily average of At- Risk behaviours from 6 months of solution roll-out.
Metric 4- Employee Productivity & Utilization :
Before SafetyConnect there was absolutely no visibility into employees distance traveled, moving hours, service center visits, time ticket resolution time. As a pioneering organisation keeping a close tab on SLA is of the highest priority to the operations team. After SafetyConnect the operations team is provided with a dashboard and many reports that give not only visibility but also eliminated manual intervention in closing the support tickets and that decreased the TAT.
ROI :
★ 73% decrease in major accidents with 6 months of solution implementation.
★ ~70% decrease in man-hours lost with 6 months of solution implementation.
★ 20% increase in safety score within 9 months of solution implementation.
Results :
Aiming at 0 major accidents, SafetyConnect could render complete visibility to the field employees driving behavior analysis, enhancing operational efficiency, and lowering man-hours, hospitalizations costs, accidents frequency leading to an increase in productivity. TA/DA payments have been associated with the daily distance travelled captured through SafetyConnect to encourage the solution usage and motivate the safe driver with better efficiency.
About SafetyConnect:
SafetyConnect helps Operations, health & safety heads of large enterprises increase productivity & safety of their plant vehicles on the in-plant roads through our best-in-class IoT-powered & analytical-driven management software.
LET’S TALK ABOUT SECURING YOUR FIELD FORCE?
Schedule a demo consultation with one of our solutions architects today!