-min.jpg)
Client’s Overview:
The client is a leading gyproc manufacturer. The company designs, manufactures and distributes materials and solutions for the construction, mobility, healthcare, and other industrial application markets.
The Client Story :
The client is a very safety-centric organization. In 2019, one major incident shook the company where-in a forklift hit an employee resulting in severe injuries in one of their plants. In response to this, the Global HQ released a forklift safety warning and they had asked all the plants across the countries to adopt a forklift safety solution which can help eliminate any such future instances.
As a result in 2020, the customer plant head rolled out SafetyConnect as a solution to address the forklift management and safety concerns. A pilot program was introduced in their plant for a duration of one month.
The Challenges :
- Multiple Touch and Hit incidents were reported due to the harsh operation of the forklifts.
- Difficulty in fleet monitoring of forklifts. There was a lack of operational visibility in the following aspects :
- Vehicle utilization
- Operator productivity.
- Inefficient driver management of forklift operators.
- Lack of Layered visibility to all the HoD’s, Plant Safety teams, and Operations teams.
The Solution :
SafetyConnect’s Forklift Safety Solution was the perfect answer to address the pain points put forth by the client. During the pilot program, we have provided -
- Fleet tracking to provide the live location of the forklifts
- Traveled path monitoring of the forklifts.
- From no visibility to vivid clarity on driving safety.
- Operators mapping for safety and performance evaluation for every forklift
- Visibility into attendance and working hours.
- Alerting mechanism for operators about journey risk beforehand, through a buzzer.
- Safety Score and unsafe event's visibility for every operator.
“Only after SafetyConnect have we identified vehicle and in-plant pedestrian risk. The derived forklift utilization helped us in planning material handling movement. Driver score and At-Risk Behaviors trends were found interesting and by using every day reports data we could have discussions with the forklift operators to improve Safety Score.”
-Plant Manager
Metric 1- Driving Behavior & User Safety Score:
The data which was collected through the devices helped the safety team to counsel the operators according to their individual driving behavior. Due to the alerting system, the operators in real-time were notified about their unsafe events, which has increased the conscious safe driving behavior of the operators. There has been a significant decrease in the Harsh events and over speeding within 7 months of the solution implementation.
The score given to each employee was not only used for counselling but also for recognizing the safest forklift operators.

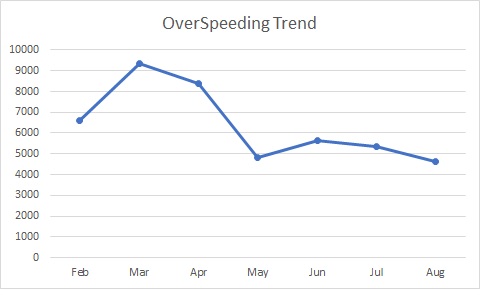
Metric 2- Fleet Management :
The live location helped the teams to locate any forklift within the plant. The traveled path of the forklifts are also provided in real-time which helped improve effectiveness of the concerned tasks and provided a platform for better management of the operational forklifts.
Metric 3- Fleet Productivity & Utilization :
Before SafetyConnect there was absolutely no visibility into the forklifts’ distance traveled, moving hours, stop time, average speed etc.
After SafetyConnect, the operations team was provided with a dashboard and many reports that give not only visibility but also helps in making analytical-driven decisions. They consider the reports generated to enhance the material handling movement. Thus, the productivity and utilization of the forklifts increased.
Overall Results :
Though avoiding incidents was the primary concern, SafetyConnect could render complete visibility to the forklifts. This has been accompanied by the benefits such as Driving behavior analysis, Driver safety, enhancing management efficiency, and lowering maintenance costs.
---------------------------------------------------------------------------------------------------------------------